Accelerating bobsleigh national team with 3D printed spike plates
BMW Group extends its technological know-how from the automotive sector to the ice track by introducing 3D-printed shoe spikes for faster bobsled starts. With Synera integrated into the process, it enables rapid, automated, and tailored creation of the 3D print data, ensuring customized spike plates in no time.
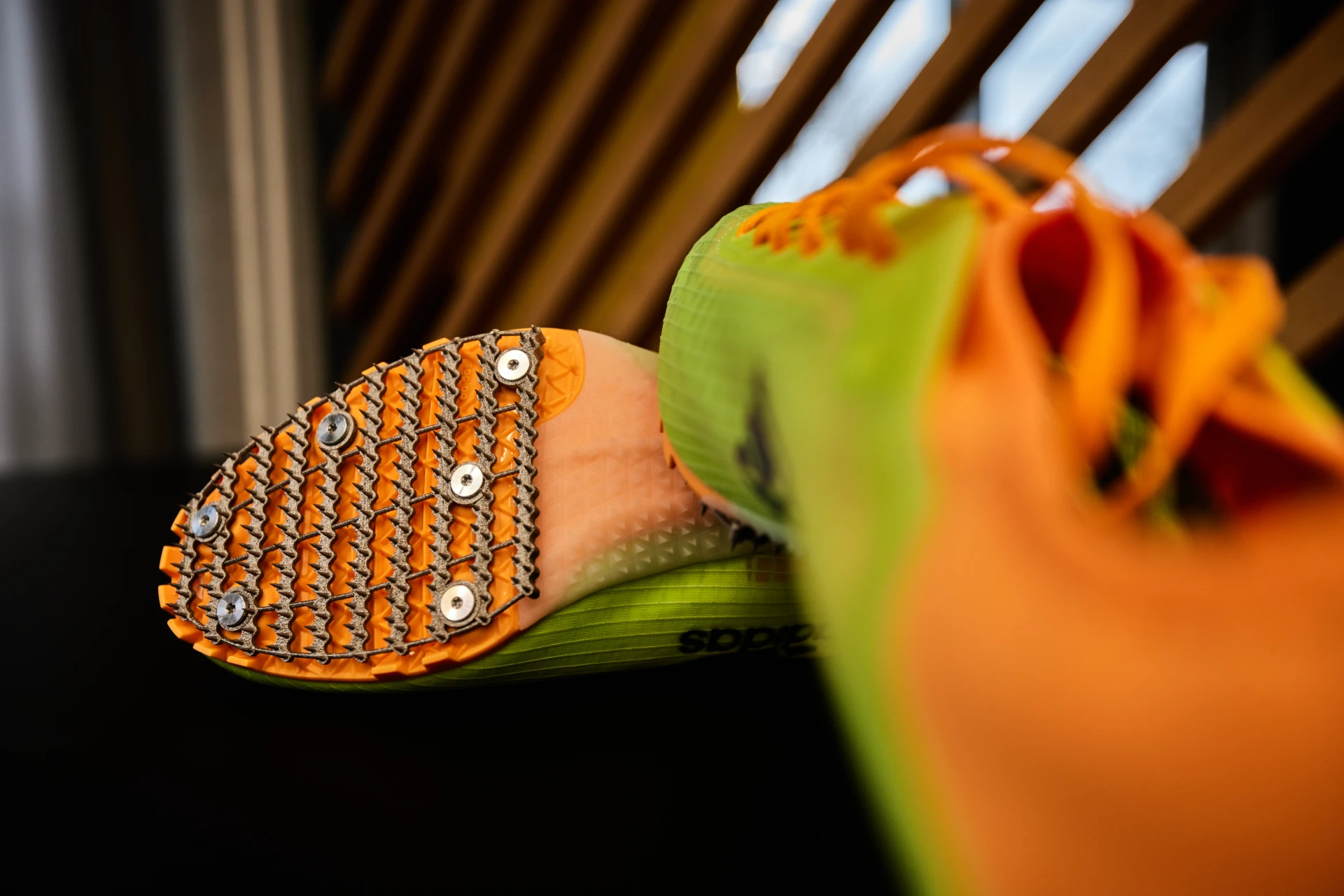
Challenge
In anticipation of the 2026 Winter Olympics, the German Bobsleigh, Luge, and Skeleton Federation (BSD) is building on its partnership with BMW Group to bring their performance standards to new heights. Leveraging BMW Group’s innovative know-how, and automotive and 3D-print expertise, the BSD aims to optimize their bobsleigh national team’s performance through customized spike plates.
Spike plates: From off-the-shelf to customized 3D prints
In the high-speed world of bobsleigh, start times are critical, determining the sled's velocity as it enters the ice channel. To maximize the athletes' pushing power, the spike plates on their footwear play a pivotal role. Traditionally, these plates were standardized, limiting customization. However, BMW Group's technology transfer from automotive development to bobsleigh has changed the game.
Utilizing 3D printing technology and Synera’s software, BMW Group has enabled the creation of individualized spike plates for each athlete. This innovative approach allows for precise customization of geometry, stiffness, and weight distribution, optimizing performance on the ice track. Unlike traditional manufacturing methods, 3D printing offers rapid prototyping and cost-effective production, ensuring that each athlete receives tailored spike plates for enhanced performance.
The biggest advantages of the 3D-print process are the saving of time and costs as well as the flexibility because no tools are required to create the components. This quickly allows us to develop, test, and efficiently optimize different variables.
BMW Group
With its brands BMW, MINI, Rolls-Royce and BMW Motorrad, the BMW Group is the world's leading manufacturer of premium automobiles and motorcycles and a provider of premium financial and mobility services. The production network of the BMW Group comprises more than 30 production locations worldwide; the company has a global sales network with representatives in more than 140 countries.
Solution
Synera’s process automation for time savings and performance improvements
The integration of Synera's software further streamlines the design process. By automating the creation of 3D print data based on individual athlete parameters, Synera ensures maximum efficiency and variability. Engineers at BMW Group can seamlessly incorporate athlete preferences into the spike plate design, resulting in significant time and cost savings, as well as customizability.
As the BSD prepares for the 2026 Winter Olympics, BMW Group continues to refine and optimize the spike plates, targeting stiffness and material selection to meet the unique needs of each athlete. With BMW's expertise in additive manufacturing and Synera's software solution, the German bobsleigh team is poised to achieve new heights of success on the international stage.
More about this workflow
Benefits
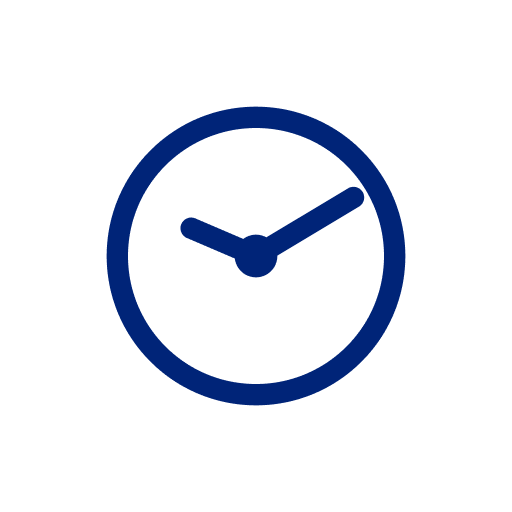
Save development time and cost through automation
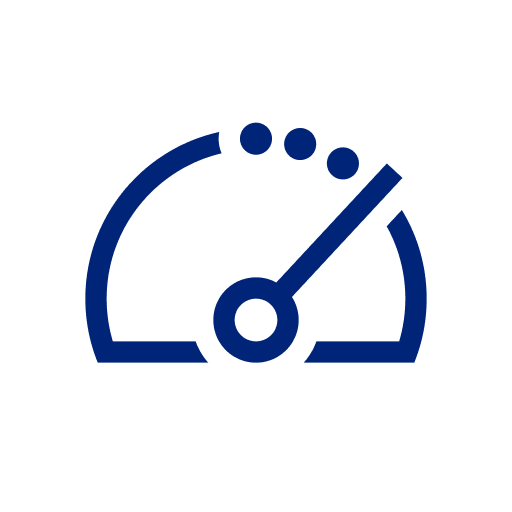
Performance improvement through customization of spike plates
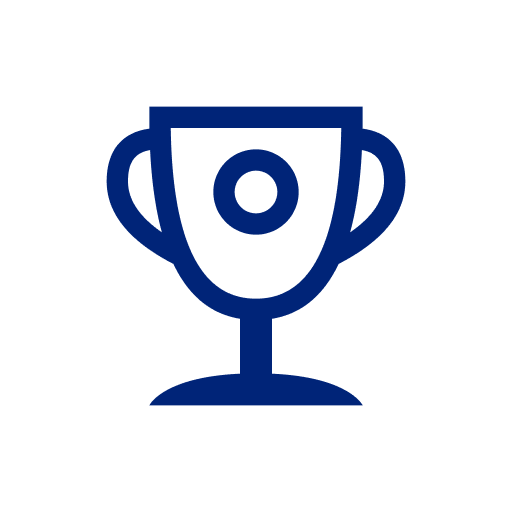
Streamlined design process for maximum efficiency