Elevating stability & efficiency for advanced parametric hairpin stator designs
The visual programming of complicated parametric CAD models is leading to a fundamental shift in hairpin stator design. Where manual design iterations previously resulted in failed models and long development times, the automated workflow integrates complex dependencies and delivers streamlined derivative creation with exceptional update stability.
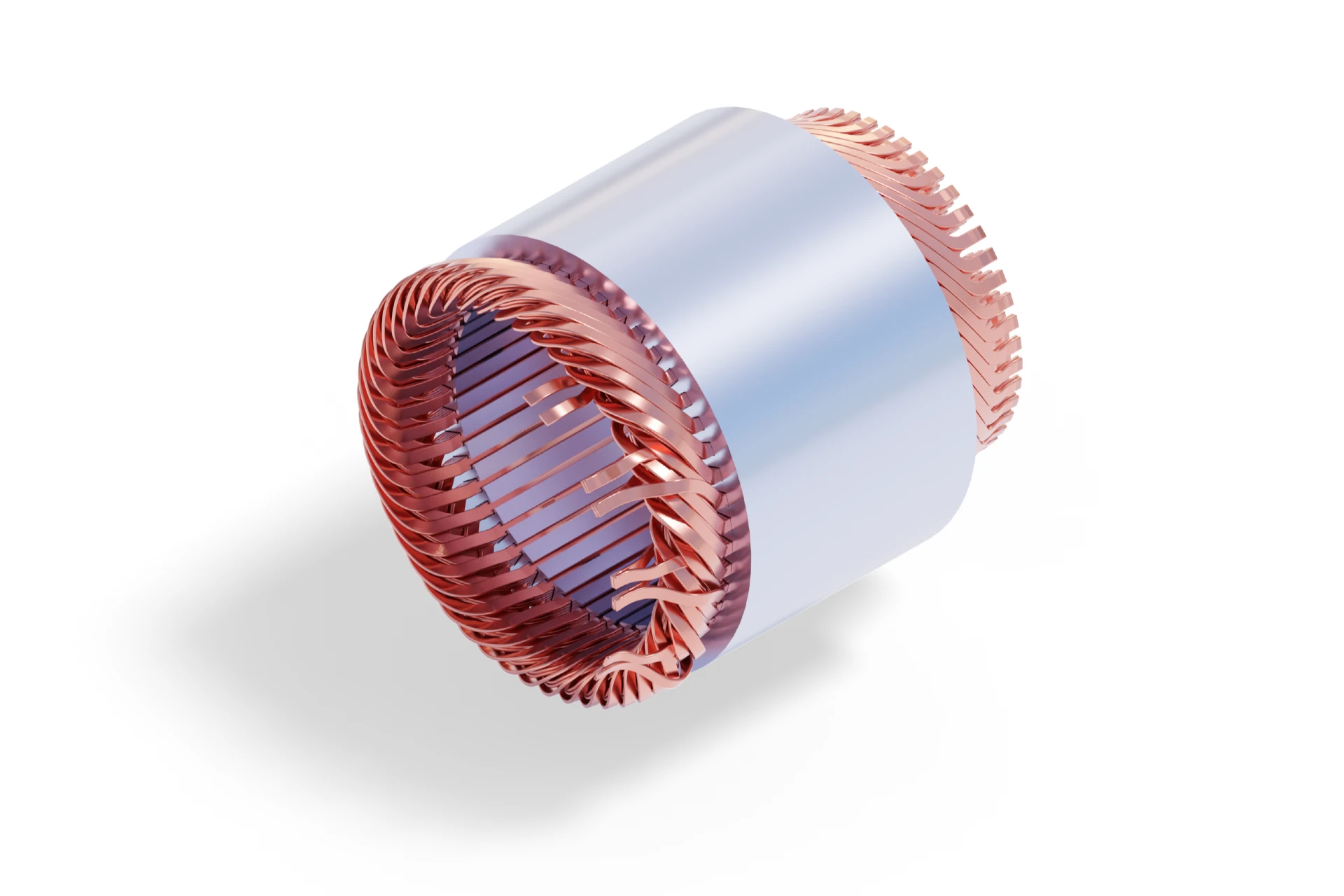
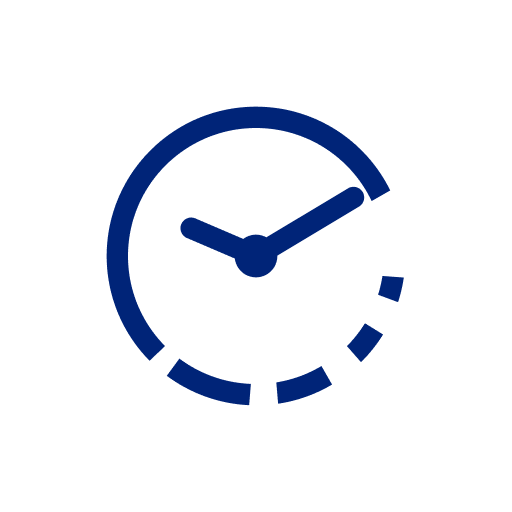
50% time savings
of whole development process incl. workflow generation
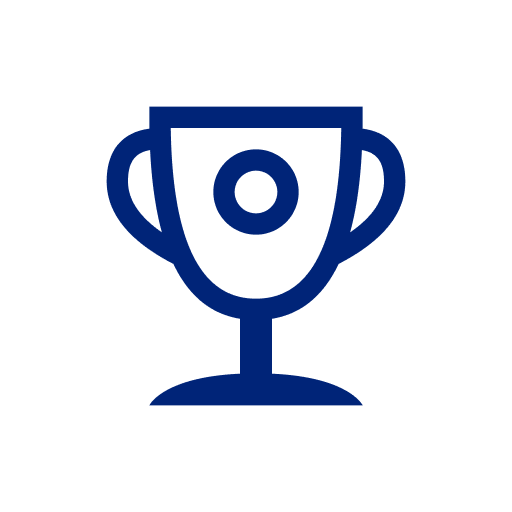
10% reduction of development cost
through process automation
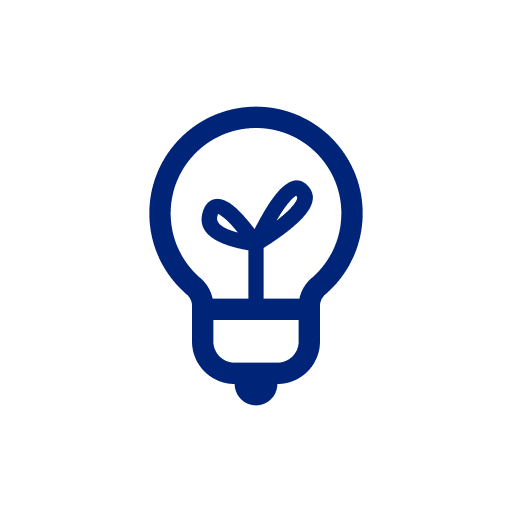
86% higher update stability
Through digitization and visual programming
Challenge
The design of electric motors is currently facing several critical challenges. Firstly, there is a pressing need to reduce the length and weight of e-motors due to very limited packaging. Secondly, the efficiency of e-drives is heavily influenced by stator winding, necessitating a reduction in losses within the copper.
Additionally, there are complexities in design, particularly at the intersection points and in connecting to the power electronics, which demand geometric feasibility. Designing the winding head presents its own set of difficulties due to the electrical winding scheme and the need for a non-symmetric solution. This complexity is further compounded as hairpin windings must navigate through narrow areas crowded with other windings for connection.
Today's product development processes exacerbate these challenges. Typically, these processes run sequentially in consecutive steps, starting with the specification of requirements and proceeding through design, evaluation, optimization, and production planning. However, these steps are often not well connected, and experts from different disciplines tend to work independently with a disconnected tool stack.
The manual description of components, surface by surface, radius by radius, in CAD software is a time-consuming task. Furthermore, the parameterization capabilities of today's CAD tools are limited, making it difficult to implement complex geometrical dependencies and fundamental geometry changes. This often results in unstable models that are prone to failure when subjected to changes and updates. The need for constant reaction to new results and changing boundary conditions requires a high level of manual effort from designers. Consequently, the process becomes lengthy and cost-intensive due to manual design and simulation steps, often yielding only a limited number of results.
"Synera reshaped how I approach hair pin stator development with integrating complex dependencies and decision gates for streamlined derivative creation. Diverse design streams enable real-time derivatives, exceptional update stability and development time reduction up to 50%."
EDAG Group
EDAG is the world's largest independent engineering provider for automotive solutions, covering Vehicle Engineering, Electric Electronics, and Production Solutions. Their diverse teams of experts shape the future of mobility, offering comprehensive engineering services from concept to product development and turnkey production systems. As a technology leader, EDAG drive innovation in lightweight construction, electromobility, digitalization, and safety.
Solution
The engineering know-how of the powertrain system experts has been digitized and visually programmed into a parametric workflow for the hair pin stator CAD design. This workflow allows complex dependencies of input and design parameters for a streamlined derivative creation and automated decision gates. To tackle the highlighted challenges, the process unfolds in a coherent and integrated manner.
Input: This phase utilizes an electrical zone plan and connection/winding scheme, typically provided in Excel format. It also considers production restrictions and boundary conditions.
Workflow: The process is divided into two key parts: the rotation symmetric part and the non-symmetric complex winding head. This involves transforming input data into geometry, ensuring compliance with boundary conditions, production restrictions, electrical requirements, and checking for geometrical intersections.
Output: The culmination of this process is the generation of optimized and feasible concept designs of stator hairpin windings, tailored to meet multi-target objectives.
The hairpin and sizing parameters like the Number of pins and layers or the overall dimensions of the design can be controlled to fully customize the e-engine. Based on that, the parametric workflow automatically creates the design of the stator body as well as the top and bottom cover based on the hairpin development which includes the pin position points and groupings. Diverse design streams and the robustness of the workflow enable real-time derivatives, excellent model stability in case of modifications, and up to a 50% reduction in development time.
More about this workflow
Benefits
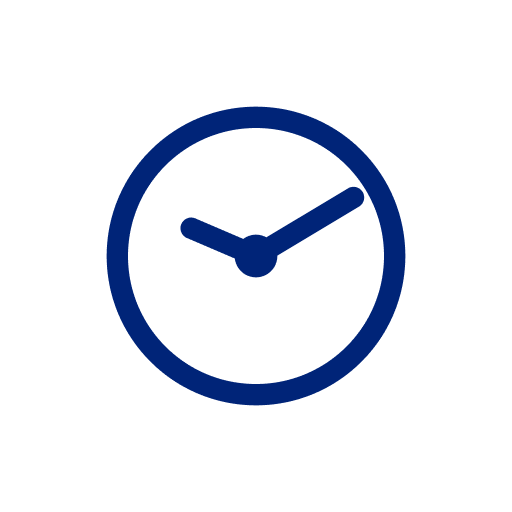
Save development time and cost through automation
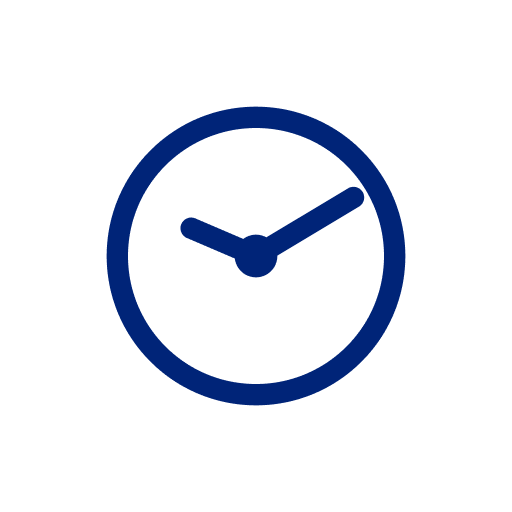
Real-time derivatives
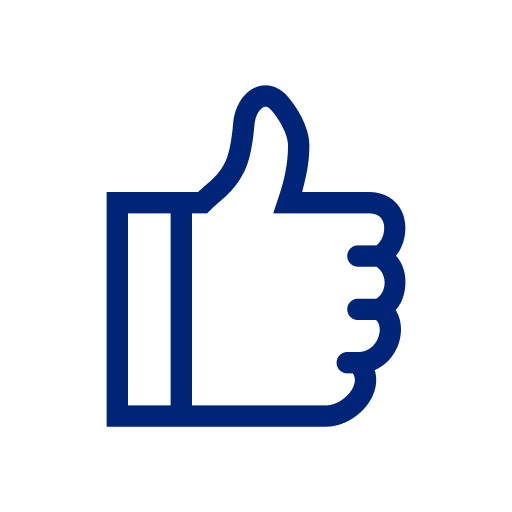
Exceptional update stability
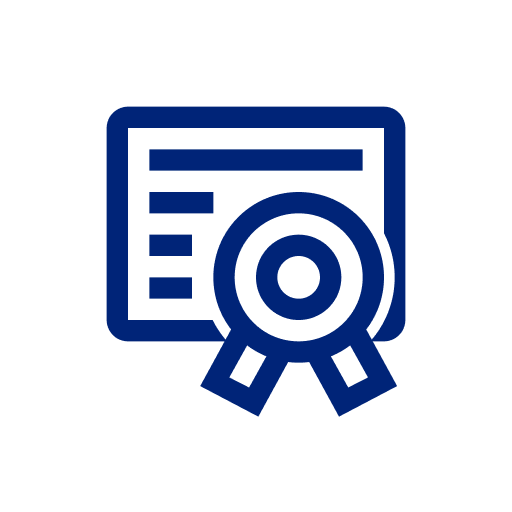
Knowledge storage through digitization of engineering
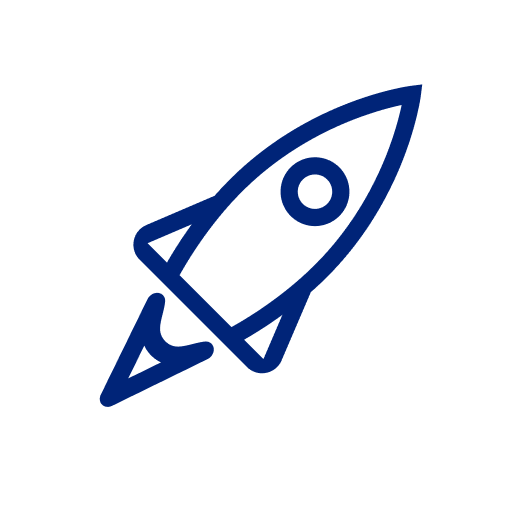
Scaling of the engineering process
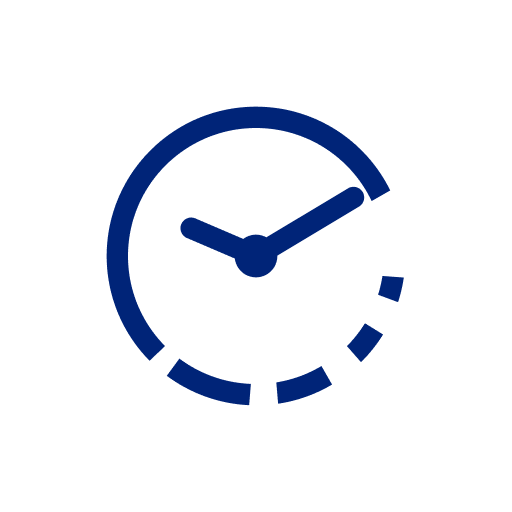
Reduction of Time-to-Market