Revolutionizing bionic design process for B-pillar
Visual programming revolutionizes Hyundai's bionic lightweight design process by combining the power of connected engineering with additive manufacturing. It ushers in a new era of vehicle structure development, provides a head start in complex optimization tasks and inspires with innovative bionic design concepts.
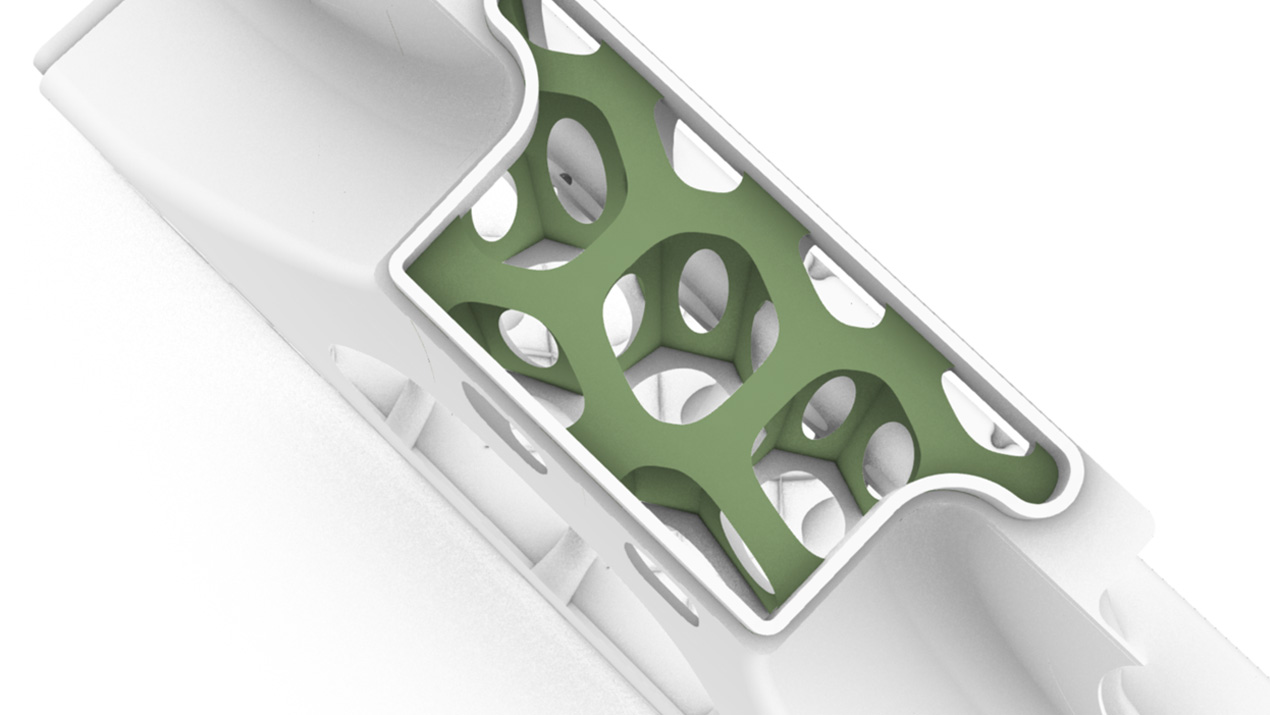
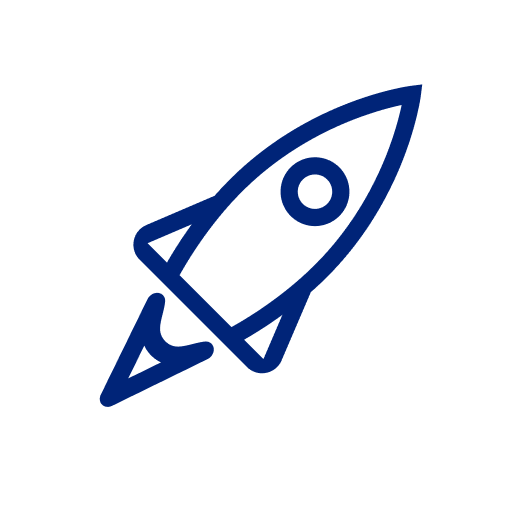
47% weight reduction
Improved performance, material usage and CO2 emissions
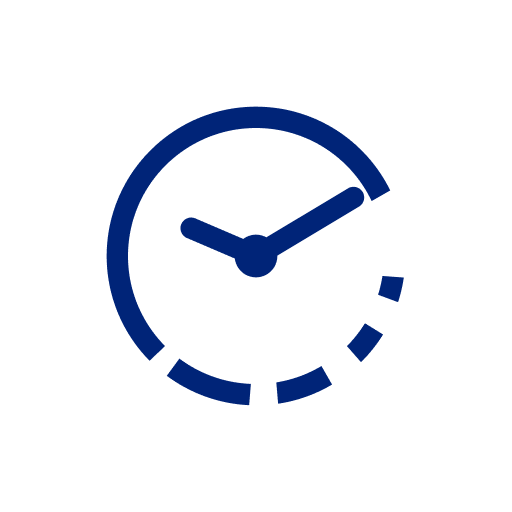
80% saved time
In comparison to the regular process
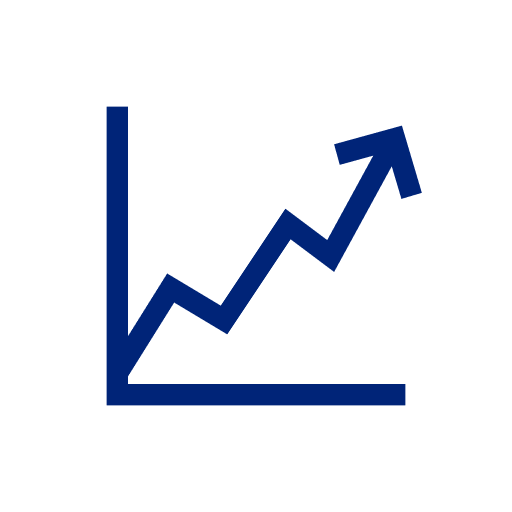
20% better performance
Reduction of the crash intrusion
Challenge
The automotive industry faces new challenges every day to meet a changing environment, such as new styling trends, scientific discoveries and stricter emissions regulations. A continuous improvement and further development of structural parts is necessary to reduce weight while improving performance and efficiency.
The B-pillar joint is one of the critical parts of the body and a particular challenge for lightweight design optimization. On the one hand, it has to meet several stringent requirements in the event of a side impact and, on the other, it has to be very stiff. Objectives that are hard to combine.
From a manufacturing perspective, additive manufacturing already offers high potential for structural lightweight design. But if the potential of design freedom is also to be taken into account, the main problem lies on the component development side. Because when Hyundai engineers face these challenges with traditional methods and software tools, the design freedom cannot be fully exploited and iterative processes between tools and development departments are tedious and slow.
Synera is a groundbreaking solution that significantly streamlines the design process for the B-Pillar node in vehicle construction. This innovative technology automates the design, eliminating the need for manual intervention. As a result, it not only reduces the effort and time required but also achieves impressive outcomes.
Hyundai Motor Europe Technical Center
HMETC (Hyundai Motor Europe Technical Center) is part of the world-renowned Hyundai, Kia and Genesis brands, and it is the company’s sole research and development center in Europe. The purpose of HMETC is to make sure that every car meets the demanding standards of the European customer and is adapted to the needs of that specific market. With the fast progress in network and technology, we strive to create the best possible solutions for a better future.
Solution
Using the connected engineering approach, Hyundai was able to digitize the development process in one workflow. This is the basis for an automated development process that takes into account the engineering experience of the involved stakeholders and departments and makes it available in real time during the engineering process. This approach itself leads to a significant reduction of the development time and effort.
The automated development process starts with the definition of input data like materials, load cases, performance criteria, manufacturing constraints and process costs. Then, the design space is defined, and all data is processed to perform a topology optimization connecting to Altair Optistruct. Based on the structural load paths, integrated bionic design algorithms create lightweight structures, specifically tailored and parametrically optimized to withstand the critical load cases. The fully parametric CAD design inside Synera and the data connection to the external software is completely automatic. So, the result is not one design but using the parameter study (Design of Experiments, DoE) at the end of the process, hundreds of different variants are created automatically by changing the input data set and design parameters.
So, the Hyundai engineers were able to use this as a head start and conduct complex crash simulations only with the two most promising design variants. After receiving the crash results, final decisions and modifications of the best design variant can then be made by the developer with only a few minor parameter tweaks. While engineers would previously have to start from scratch every time a change was made, this automated approach requires no manual intervention in the design and not only results in a higher-performing part. The workflow handles the complexity of multiple optimization objectives with ease, resulting in a higher performing part and significantly reducing development time. Ultimately, Hyundai's partnership with Synera has set the stage for streamlined automotive design, illustrating the transformative potential of visual programming in engineering.
More about this workflow
Benefits
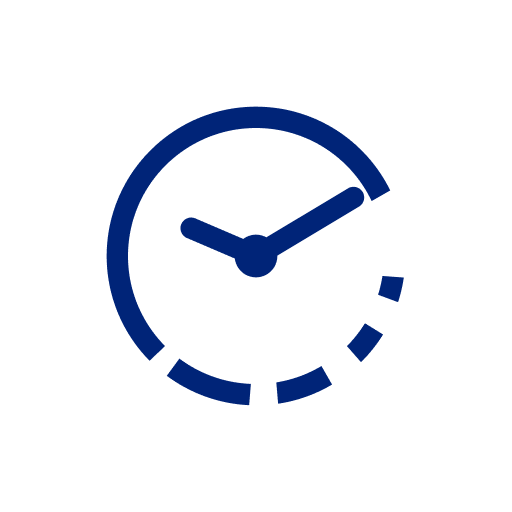
Reduction of Time-to-Market
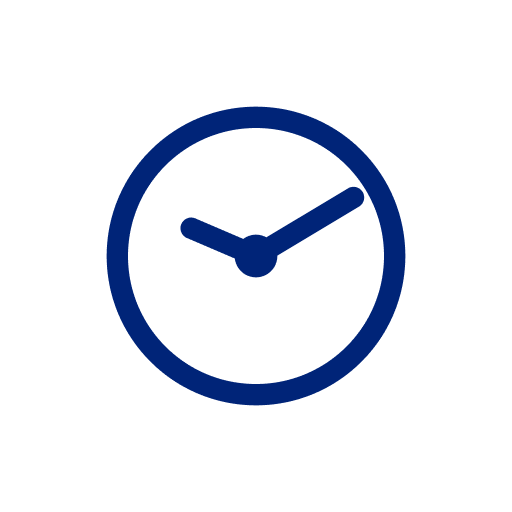
Save development time and cost through automation
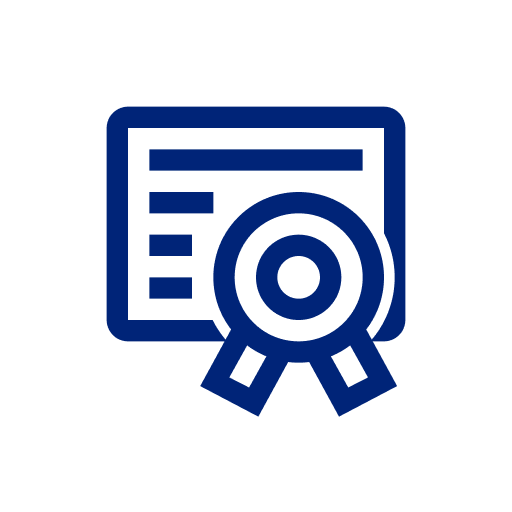
Knowledge storage through digitization of engineering
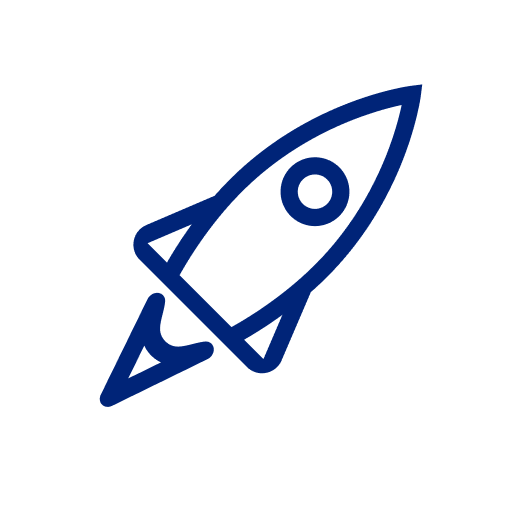
Scaling of the engineering process
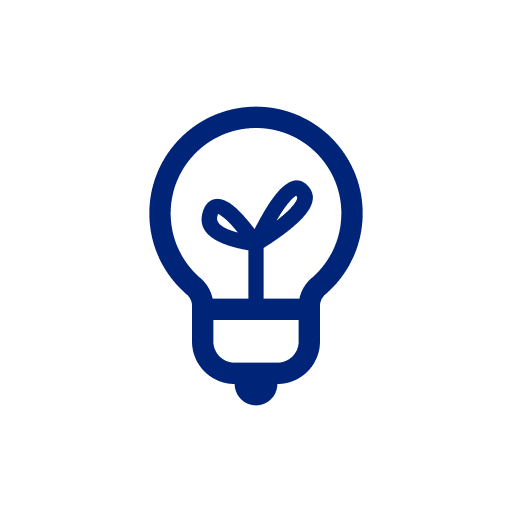
Innovative concepts through algorithmic design