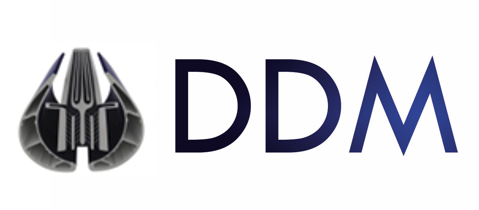
Generation of Shell models for investment casting
DDM Systems pioneers complex metal investment castings with the unique DirectPour™ process and patented LAMP™ 3D printing technology. By directly pouring metal into ceramic shells, DDM slashs costs and time compared to traditional methods, all without upfront tooling investment. Yet, creating these intricate ceramic shells remains a labor- intensive task. Synera streamlines ceramic shell generation with advanced features like mesh manipulation, field-based design, and lattice structures. Using LAMP technology and a Synera-based workflow, DDM simplifies ceramic shell creation, eliminating multiple steps and reducing lead time.
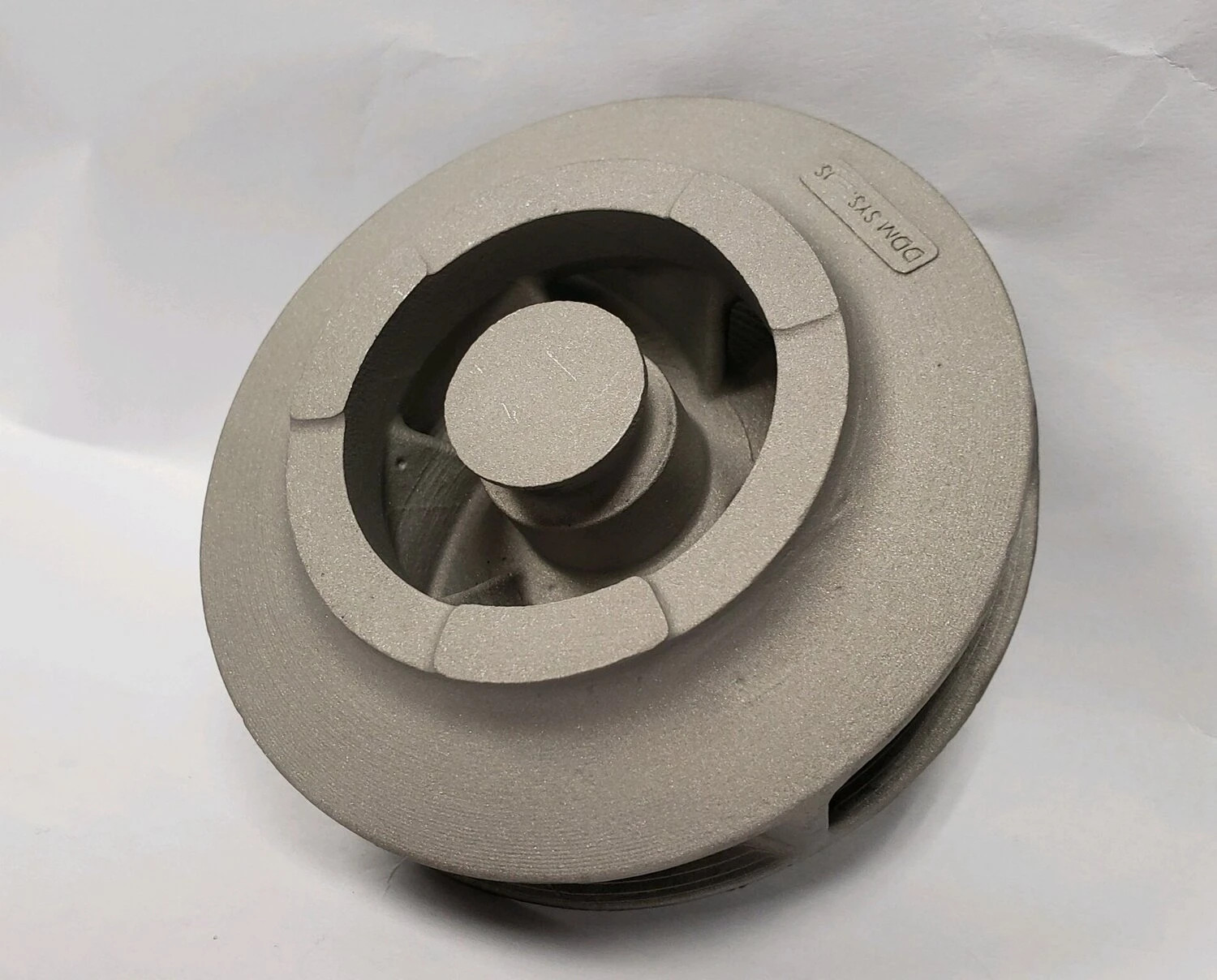
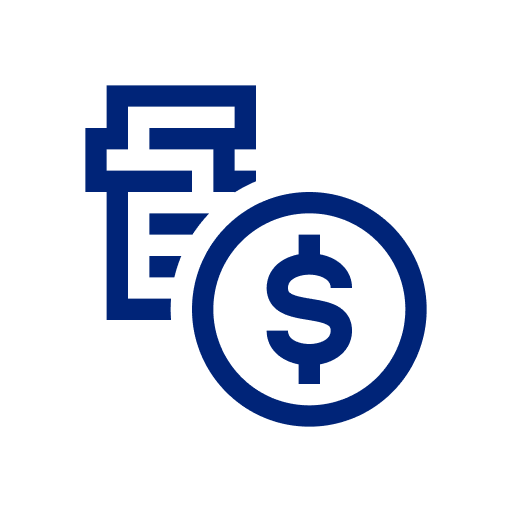
ROI of 350% percent
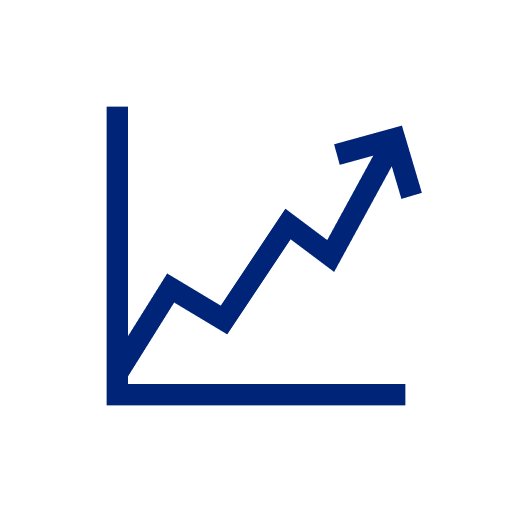
80% reduction of manual steps in design of casting shell models
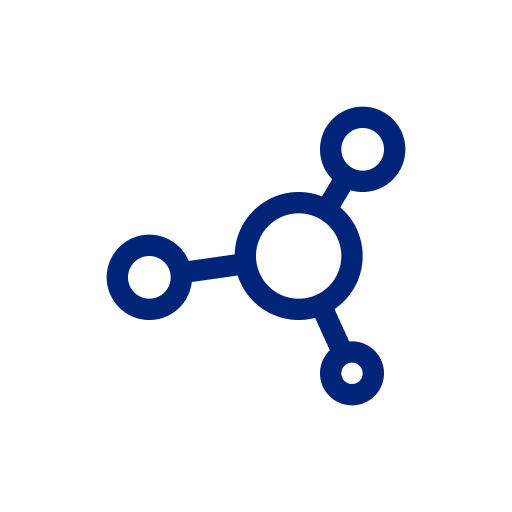
Possibility to combine various technologies within one platform for optimal design
Synera streamlines casting shell model design by integrating various technologies into one platform. This eliminates the need for switching between multiple tools, thereby saving time and improving model quality through seamless collaboration among experts.
DDM Systems
DDM Systems, founded in 2012 in Atlanta by Suman Das and John Halloran, advances aerospace and turbine industries with LAMP™ and SLE™. LAMP™ enables tool-less ceramic core manufacturing for investment casting, while SLE™ innovates repair and production of turbine components with non-weldable superalloys.